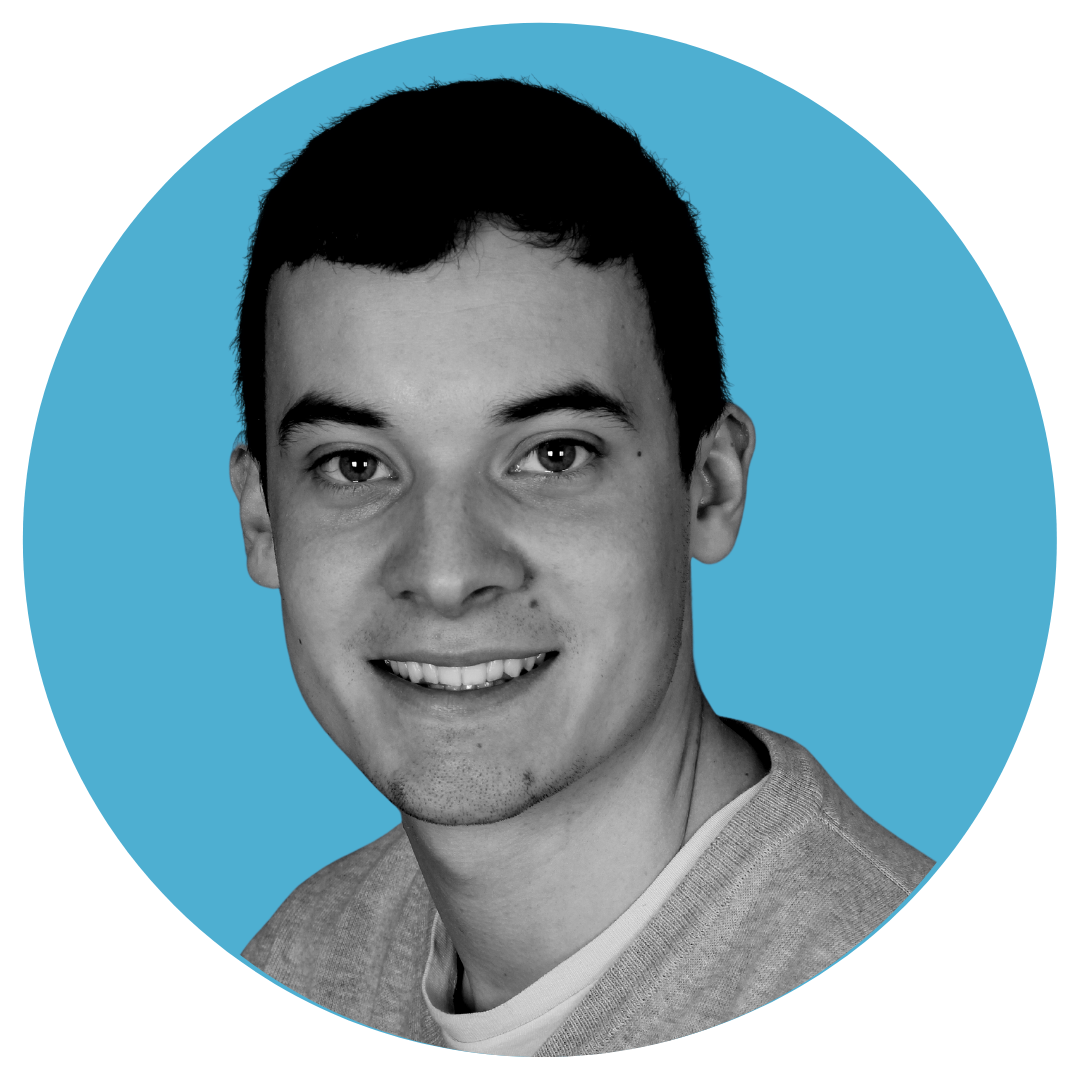
Kyle McRobert
Automotive Physical Layer Testing
How does Quarch fit into the automotive testing industry? We have been the industry standard for physical layer testing across a range of industries, such as drive manufacturing, data storage systems, networking, telecommunications, and more, for over 15 years.
Automated vehicles have very similar failure scenarios to enterprise-class data storage systems, but the failure cases can now result in injury or death. Hence, automated physical layer testing returns invaluable data. Modern vehicles can be mounted with well over 100 sensors of various types, ranging from safety-critical to user comfort.
Sensors such as wheel speed, radar, lidar, the physical position of parts, pressures, and temperatures. These all need to talk to control units (ECU’s etc) and can use a range of protocols to do so.
Quarch already has a range of products, such as our high-speed LAN, PCIe, and USB-3 breakers, that can be used for automotive applications. However, one of our latest products is more targeted towards the automotive sector and supports a whole host of protocols.
The Automotive Breaker (QTL2602) is a versatile standalone fault injection and monitoring device. Using a simple pluggable terminal block, this product connects to a wiring loom. It has a power channel capable of switching up to 15V DC up to 8A and 4 data channels able to switch signals with a bandwidth of 460MHz and a voltage range from -15V to 15V. This means it supports a large range of protocols, such as SPI, I2C, RS232, CAN, 100/1000Base-T1 and more. In addition to fault injection, we can monitor the signals in real-time and record them for later analysis (limited to a sample rate of 1MHz for monitoring the signals).
When in place, we can create physical layer interruptions, from short data glitches to permanent failures. This means we can do faults you would see with damaged connectors, pin bouncing from vibrations, complete failure of sensors and more. This allows our customers to prove that their links are fault-tolerant and have appropriate redundancies.
It is common in the automotive industry, to use EMI (Electro Magnetic Interference) techniques to inject errors into data links. While this is useful, it does not cover all the possible failure cases that can occur during the life of a vehicle
Automotive Testing Terms – An Introduction
CAN Bus practical example
One of the best ways to understand how our products work is to run through a simple example. We will run through one of the most basic tests we could use the breaker modules for, which is to hot plug a device. In this example, we will use the breaker module (QTL2602) to hot plug an OBD (On-Board Diagnostics) reader into the ODB port of a car. This reader communicates to an ECU (Engine Control Unit) using the CAN Bus and is powered by 12V from the ODB port. We achieve this by cutting the cable to the ODB reader and sitting between the ODB reader and ODB port (figure 2).
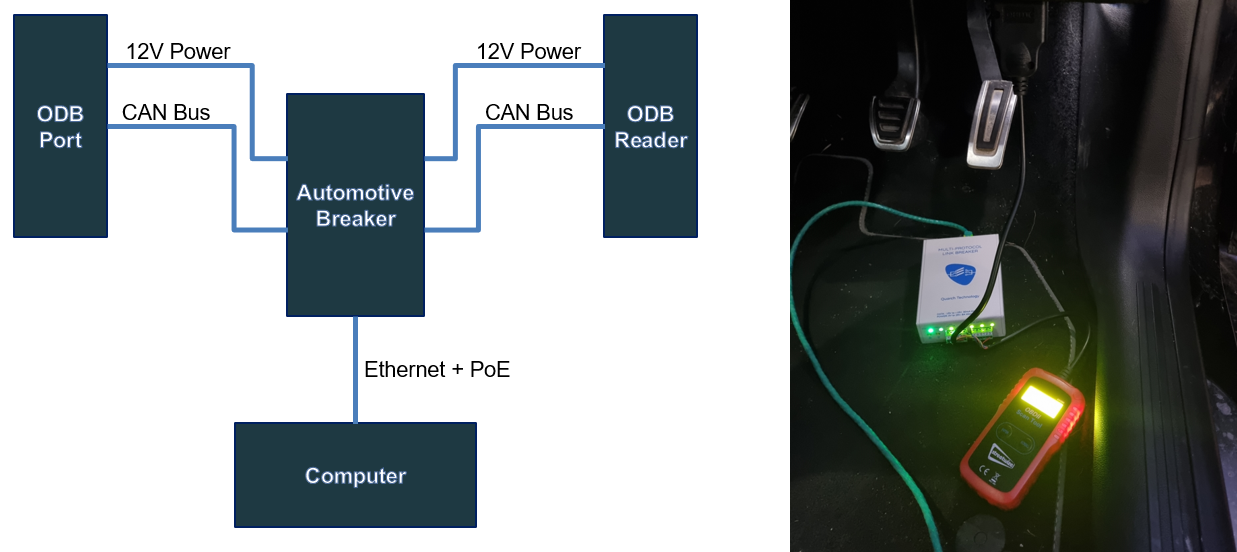
We can interface with Quarch products in various ways. In this example, we use a Python script to run our test, which does the following:
- Configures the Breaker Module
- Connects to the Breaker Module.
- Sets thresholds to allow us to capture the CAN Bus trace.
- Set timings for each connection in the hot plug.
- Starts a QPS (Quarch Power Studio) stream.
- Polls host and device voltage levels, adding these as custom channels to the stream.
- Performs the hot plug (connecting the data bus)
- Ends the QPS stream.
After running, we get the following:
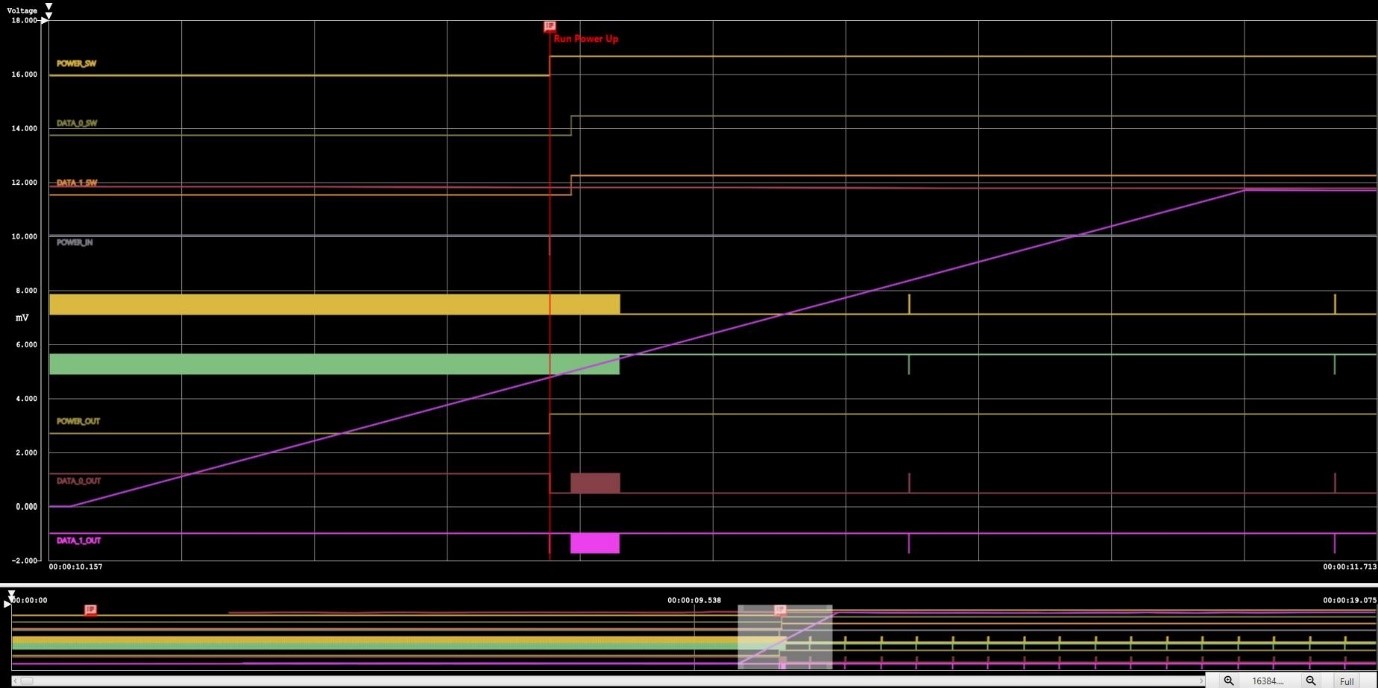
This is the QPS view of the simple hot plug test running at 1MHz sampling, allowing us to capture the CAN Bus packets. The script also annotates when the hot plug happened. We can see the purple line on the graph. This is our custom channel showing what the device voltage is doing. We can save this trace for analysis later, or send it to others to examine. Zoom into any part of the timeline to see what happens on both host and device side during the hot plug, as shown below.
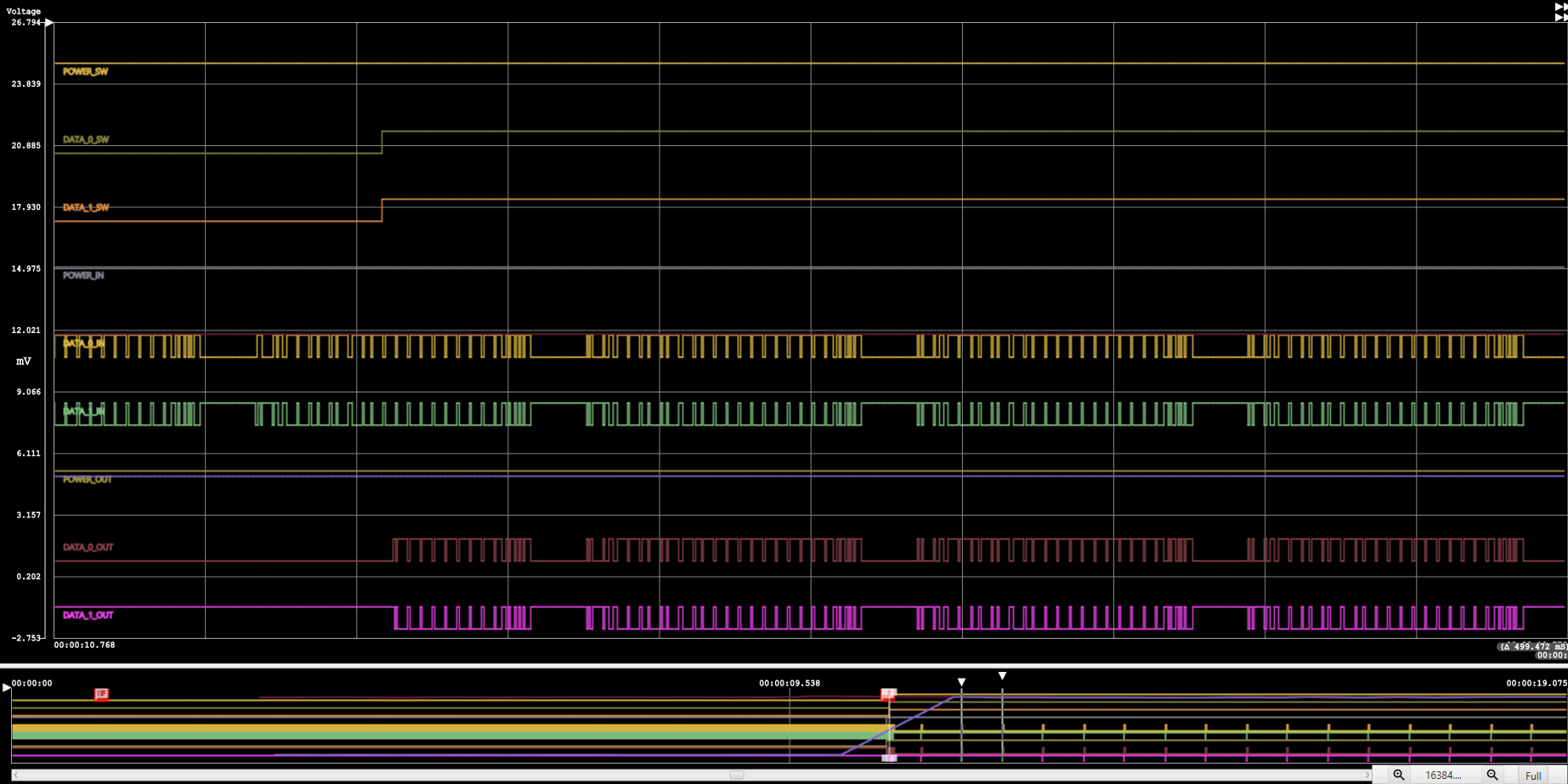
Data interruption
There are many more tests we can run, a common one being to ‘glitch’ or briefly interrupt the data. This would happen in the real world when vibration or water penetration caused brief interruptions to the physical bus. Injecting these faults is simple and can corrupt or block data packets, testing the integrity and recovery of the bus.
To evaluate this product or for more information, visit here.